Roughly half of the 45 million tonnes of fibre consumed annually in the world are now made from synthetic polymers.
While the tonnage of man-made cellulosics sold into European nonwovens has held remarkably constant for 30 or more years, viscose rayon has participated hardly at all in the massive growth of the industry and its market share is now a tenth of the 1970 figure.
Viscose rayon staple fibres were, in 1966, the cheapest man-made fibre. Now they are around twice the price of the main synthetics without the ability to be easily spun-laid or thermally bonded. At a time when the premium obtainable for biodegradability is almost non-existent, they are currently out of contention as a source of economic biodegradable coverstock.
We therefore need to examine the potential of new routes to biodegradable nonwovens and will do this in two parts. We will start by reviewing recent developments in biodegradable synthetic fibres and then return to look at new routes to cellulosic nonwovens that may be capable of yielding major cost savings.
Biodegradable Synthetics
Biodegradation of fibres occurs when their constituent polymers are depolymerised, usually by the action of enzymes secreted by microorganisms. These enzymes act by hydrolysing or oxidising the polymer, and can work on the ends of the chains (exo-enzymes) or randomly along their length (endo-enzymes). To do its work, the enzyme has to be able to bond to the fibre and gain access to sites capable of being oxidised or hydrolysed. The most biodegradable fibres therefore tend to be hydrophilic, and made up of short, flexible chains with low levels of crystallisation. They will often have chain backbones with oxygen or nitrogen links and/or pendant groups containing oxygen or nitrogen atoms. This description clearly fits most natural fibres and fibres made of natural polymers.
Biodegradation-resistant polymers have the opposite characteristics and unsurprisingly are used to make the stronger more durable fibres. Oxygen-free polymers such as polypropylene and polyethylene resist biodegradation totally.
Polyester (i.e. the aromatic polyethylene terephthalate), despite its oxygen content is degradation resistant probably because it has rigid, rod-like chains. The same is true for polyamides despite their nitrogen content.
Unlike the aromatics, aliphatic polyesters are generally biodegradable. More than a hundred species of bacteria are known to synthesise and store aliphatic polyesters for future use as an energy source. While being naturally biodegradable, these polyesters are also thermoplastic and capable of being extracted and formed into films and fibres like any other polyester.
Man-made biodegradable aliphatic polyesters are however still based mainly on the industrial polymerisation of monomers such as glycolic acid (PGA), lactic acid (PLA), butyric acid (PHB), valeric acid (PHV) and caprolactone (PCL). These (Fig. 1) and their copolymers have already found application in implants, absorbable sutures, controlled release packaging and degradable films and mouldings 1.

Fig. 1. Biodegradable aliphatic polyesters
Thanks to massive investment announced this year by Cargill Dow LLC, the PLA variety currently look most likely to meet our requirement for a low cost biodegradable coverstock.
Polylactic Acid Fibres
Polylactic acid was first made in 1932 by Carothers, who developed a process involving the direct condensation polymerisation of lactic acid in solvents under high vacuum. He abandoned the polymer as too low in melting point for fibres and textiles and went on to develop nylon.
More recently PLA was developed as an alternative binder for cellulosic nonwovens because of its easy hydrolytic degradability compared with polyvinyl acetate or ethylene-acrylic acid copolymers .
Spunlaid and meltblown nonwovens based on PLA were researched at the University of Tennessee Knoxville in 1993 (3).
Kanebo (Japan) introduced Lactron® (poly L-Lactide) fibre and spun-laid nonwovens in 1994 claiming a capacity of 2000 tpa being expanded to 3000 tpa. It targeted agricultural applications to start with, and in 1998 was re-launched for apparel end-uses. At that time, Japanese demand for PLA fibres was said to be 500-1000 tpa. In order to improve the biodegradability and reduce the costs of the nonwovens, blends with rayon were also developed.
Fiberweb (France) disclosed nonwoven webs and laminates made of 100% PLA in 1997 (4) and introduced a range of melt-blown and spunlaid PLA fabrics under the Deposa brandname (5). The polymer was developed by Neste Oy.
Galactic Laboratories (Belgium) provided an excellent overview of polylactic acid polymers (6), concluding that 390,000 tonnes of the polymer would be produced by 2008 at prices around $2/kg. Their estimate of 70,000 tonnes for 2002 looks about right with the new Cargill-Dow plant due to start during that year. It remains to be seen if the price will be right also.
Cargill Dow Polymers LLC, now the leader in polylactic acid technology is a 50/50 JV between Cargill and Dow formed in November 1997. They currently have 4000 tpa capacity for the polymer EcoPLA, and plan to double it this year "to meet immediate market development needs". In January this year they also announced the construction of a 140,000 tpa plant to make NatureWorks PLA ,"a family of polymers derived entirely from annually renewable resources with the cost performance necessary to compete with traditional fibres and packaging materials" (7).
The plant is due to start up in 2002 and several fibre companies are already producing fibres from the new polymer. (Fibre Innovation Technologies, Parkdale, Unifi, Interface, Woolmark, Unitika, Kanebo and Kuraray are mentioned as "Development Allies").
Their process (8) involves extracting sugars (mainly dextrose, but also glucose and saccharose) from cornstarch, sugar beet or wheat starch and then fermenting it to lactic acid. Refined sugars are preferred to the cheaper molasses or whey because purification after fermentation is more expensive.
The lactic acid is converted into the dimer or lactide which is purified and polymerised (ring opening method) to polylactic acid without the need for solvents (Fig. 2). The family of polymers arises in part from the stereochemistry of lactic acid and its dimer. As fermented, lactic acid is 99.5% L-isomer and 0.5% D-isomer.
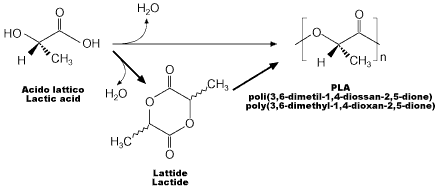
Fig. 2. Direct and Dimer Routes to PLA 8
Conversion of this to the dimer can be controlled to give three forms, the L, D, and Mesolactides. (Fig. 3)
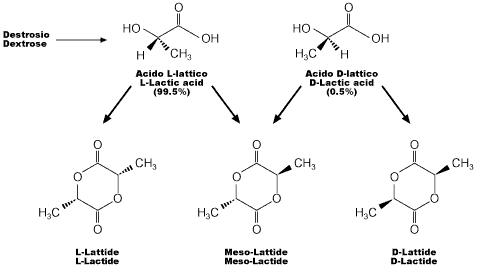
Fig. 3. Three different lactides are possible 8
Polymerisation of the lactide to give polymers rich in the L-form gives crystalline products, whereas those rich in the D-form (>15%) are more amorphous. The enhanced control of the stereochemistry achieved in the dimer route accounts for the superiority of the current products over those from the 1932 Carothers approach. The resulting PLA resin can be extruded like other
thermoplastic resins to make fibres, films, spunbonds etc.
Fibres from the first mentioned EcoPLA polymer were said to be:
- Reminiscent of PET or PS in some forms and of PP and PE in others.
- Fully biodegradable under composting conditions.
- Convertible into nonwovens by dry- air- wet- spunmelt- laying systems.
- Capable of giving improved resilience, moisture transport, breathability and wet strength.
- The price was, in 1998, said to be $3-6/kg, but capable of reduction to $1.1/kg at full-scale production.
Additional claims for NatureWorks recently announced were:
- Value-added natural-based fibres.
- Bridges the gap between silk, wool, cotton and the synthetics.
- Superior handle and touch.
- The comfort of natural fibres with the performance of synthetics.
- Controlled degradability, enhanced wicking, low linting.
- Excellent UV resistance and elastic recovery.
- Reduced flammability with low smoke and heat generation.
Nonwoven applications were listed: fibrefill, crop covers, geotextiles, wipes, hygiene, medical, diapers and binder fibres.
Clearly PLA can be manufactured with a range of properties, if only because the lactic acid, being chiral and with two asymmetry centres exists in four different forms. It also appears to have the properties required to meet our biodegradable diaper requirements, being easily converted into film, fibre, spunbond and meltblown products on existing extrusion equipment.
However the new 140,000 tonne polymer plant is said to be costing $300 million so whether or not the polymer can be produced down to a price that would guarantee success, i.e. <50 c/lb (similar to PP and PET resin prices) remains to be seen.
Several other producers are active. At Index 99, NKK (Japan) showed a PLA spunbond nonwoven at 15 gsm with apparently excellent formation and properties. Kuraray (Japan) showed PLA fibres and provided some data on their properties and biodegradation rates. PLA polymer is made in Japan by Mitsui Toatsu (under the Lacea brandname; unlike CDP, MT process polymerises the lactic acid direct from the monomer), Toyobo, Dai-Nippon Ink Chemicals, Showa Polymers and Shimadzu Corp.
Biodegradable Fibre Properties
A comparison of readily available published data is provided in the Table below.
Property |
CDP PLA |
Kuraray PLA |
Rayon |
Lyocell |
Polyester |
Density (g/cm3) |
1.25 |
1.27 |
1.51 |
1.52 |
1.38 |
Melting Point (°C) |
120-170 |
170 |
None |
None |
260 |
Count (dtex) |
1.7 (e.g.) |
1.7 |
1.7 |
1.7 |
1.7 |
Tenacity (cN/tex) |
50 |
25-45 |
20-25 |
40-45 |
35-65 |
Elongation (%) |
35 |
N/A |
18-22 |
14-16 |
15-40 |
Moisture Regain (%) |
0.4 - 0.6 |
0.48 |
13 |
12 |
0.4 |
On the information currently available, PLA looks like an excellent fibre with the right technical credentials to replace polypropylene in nonwovens. As noted by Carothers, the melting point still appears too low for it to challenge the supremacy of aromatic polyester in mainstream textiles.
Other Biodegradable Synthetics
Monsanto's BIOPOL (originally developed by ICI-Zeneca (9), who planned a 10,000 tpa plant in 1987) was based on a random copolymer of 3-hydroxybutyrate and 3-hydroxyvalerate made by bacterial fermentation. It was sold for around $15/kg for speciality products and was expected to appear in fibre form at a much lower price. At Index 99 Monsanto was said to have stopped the project in Jan 1999. However their press release in October 99 notes (10) that direct production of PHBV and other poly(hydroxyalkanoates) in plants, the latter said to be viable alternatives to expensive fermentation processes.
Polycaprolactone has been used in blend with other plastics to make biodegradable films since the late 1970's. Unitika and Nippon Unicar developed a hydroentangled nonwoven based on 80% cellulose and 20% PCL fibres (11). Freudenberg (Germany) developed biodegradable spunbonds based on 50% PCL and 50% "conventional fibre forming polymer" for scrub-suits, incontinence products and bandage holders (12).
Bayer's BAK, a polyester amide polymer is based on hexamethylene diamine, butane diol and adipic acid. Butane diol is also the basis for Bionolle, Showa Polymer's biodegradable synthetic.
Eastman's Eastar Bio is a copolyester based on terephthalic acid and ethylene glycol.
Dupont's Biomax is said to be based on 3 proprietary aliphatic polyesters and costs only slightly more than conventional PET.
Procter and Gamble described (13) a process using the Biopol-type polymer (or other biodegradable synthetic) either melted or dissolved in solvent and then blown or flash-spun into a microfibre nonwoven, either alone or in blend with a variety of natural fibres. A continuation patent published this year (14) relates to a biodegradable poly(hydroxyalkanoate) for both diaper topsheet and backsheet.
Spun-Laid Cellulosics
All evidence to date suggests that biodegradation will only become a major marketing issue if it can be delivered in a diaper without sacrificing any of the attributes of the current leading brands.
Biodegradable nonwovens usable as coverstocks already exist in many forms, one of the best being hydroentangled rayon, but none are available at a price to compete with thermal bonded spun-laid or dry-laid polypropylene. Furthermore to perform as well as PP in wet-back testing the HE rayon would need an additional finishing process.
If we consider the cost of cellulosic nonwoven at the converter, the greatest savings can in theory be achieved by moving from dry-laying staple fibres to a suitably sized spun-laying operation in a fibre plant, ideally on the site of a pulp mill. Much work has already been done in this field, most of it before environmental issues such as biodegradation and renewable resources had reached the public consciousness.
Viscose-Cupro Routes
Several cellulosic fibre producers have already attempted to improve the performance/cost ratio by making nonwovens themselves.
- Courtaulds (now Acordis), Rhone-Poulenc and Enka Glanstoff AG (now Acordis) developed spun-laid rayon nonwovens on a pilot scale in the late 60's and early seventies.
Courtaulds relaunched an improved fabric based on a new process in 1978 and withdrew in 1982.
- Kanebo and Daiwabo researched similar techniques.
- Asahi worked with viscose and cuprammonium pilot lines before commercialising the cupro route as Bemliese® nonwovens.
- Mitsubishi Rayon developed a process (later sold to Futamura) based on hydroxymethyl cellulose xanthate in which the webs were point-bonded in a thermal calender before regeneration.
- Kosabura Miura spun viscose vertically downwards from oscillating spinnerettes onto a conveyor, and oversprayed the liquid filaments with acid.
- The Tachikawa Research Institute developed a polynosic viscose spun-laid process.
The surviving processes, Asahi's Bemliese® and Futamura's TCF®, both make coverstock weights but on a relatively small scale and at premium prices. In fact there's nothing here to persuade today's diaper manufacturers that these cellulose based spun-laid processes could be a viable contender for a biodegradable coverstock.
Maybe the sort of visionary thinking now evident in the Super-Site concept (pre-forming diaper cores by air-laying them on 100,000 tpa machines based at a pulp production site (15) could dramatically reduce the costs of a viscose-based spun-laid fabric? The viscose process is however being superseded by other more environmentally "benign" routes to cellulosic fibres and it is these processes that we should now turn to.
Of the numerous other routes to cellulosic fibres researched in the last 3 decades, within the context of this paper, four are worth mentioning. All have been developed primarily to make fibres for conventional textiles and may well have evolved differently had a market the size of coverstock been an attractive development target. All appear to be more amenable to integration with pulp production than the viscose route.
The Carbamate route
Turunen (16) and Struszczyk (17) reacted cellulose with urea to form a stable derivatised "pulp" which could be stored indefinitely and was easily dissolved in sodium hydroxide. The resulting solution was also spinnable into dilute acid or alkali to yield fibres of cellulose carbamate or regenerated cellulose (or mixtures of the two). From our current point of view, the cellulose carbamate fibres themselves appear more interesting:
- Fibres with a nitrogen content of 2% resisted biodegradation without being toxic to the organisms. They also had high water absorbency and were soluble in 8% caustic soda. They were self-bonding when wet-laid.
- Fibres became progressively more biodegradable and insoluble in alkali as the nitrogen content was reduced (and the cellulose regenerated).
The process was operated on a pilot scale by Saeteri (Finland) and small amounts of fibre were evaluated in nonwovens, but as far as this author can ascertain, never in spunbonded nonwovens.
Taking this and the "Super-Site" thinking, the pulp-mill would supply not only the fluff-pulp for air-laid cores but also the carbamate pulp for coverstock manufacture. Coverstock would be spunlaid on site allowing economic recovery and recycling of the process chemicals. The basic cellulosic spumbond could be finished to make topsheet, backsheet or acquisition layers.
In the more conservative world of fibres for textiles, carbamate's properties were less desirable than those of the next process to consider: dissolution and regeneration of cellulose from amine oxide solution.
The Lyocell Route
Employing the cyclic amine n-methyl morpholine n-oxide to dissolve cellulose prior to spinning the dope into water, the Lyocell process has been fully developed and scaled up for textile applications by Enka and Courtaulds (now together in Acordis) over the last 20 years.
It offers an environmentally acceptable way of converting natural cellulose into a fully biodegradable premium quality rayon fibre with tensile properties approaching those of polyester.
Furthermore the technology offers the potential for converting pulp to fibre on a scale and at a cost that would give polyester and cotton some serious competition.
The high capital requirement of the first plant necessitated launching the fibre (in 1990) at a premium price into the fashion-apparel market. This proved highly successful and led to rapid expansion up to the current capacity of around 100,000 tonnes. However this represents only about one half of one percent of the current cellulosic fibres market, and Lyocell fibre is still only available commercially from two sources, Acordis and Lenzing (Alceru (Schwarza), FCFC (Taiwan), Hanil Synthetic Fibre Co. (Korea), and the Birla Group (India) are all working with Lyocell pilot plants). Only Lenzing appear to have had even the theoretical capability of integrating lyocell with pulp production, and have chosen not to.
Lyocell makes excellent nonwovens, especially in those processes that allow it's superior aesthetics to shine through, like needle-punching and hydroentanglement. Its high strength is of little intrinsic value in disposables, but it enables the nonwoven producer to reduce basis weight while meeting strength targets. It's freedom from shrinkage and high wet stability allows higher area yields in HE processes, and its high modulus prevents it from collapsing in the wet to the same extent as viscose rayon. Fibrillation, the development of surface microfibres on wet abrasion or in high-pressure entanglement, adds an additional dimension for the nonwoven developer. Unfortunately, while it has established itself in several profitable niches, its premium positioning has so far prevented it's use in mainstream disposables.
The nonwoven industry enjoys the economies of polypropylene because PP is a by-product of the energy industry. Viscose rayon requires dissolving pulp, a premium product of the timber industry. Lyocell is currently similar, but its simple production process has the so far unexplored potential to use cheaper pulps and hence the potential to achieve the economies of scale that may ultimately interest the major diaper producers.
The key development of making lyocell from cheaper pulps and spunlaying it is described in a recent Weyerhauser patent (18). Here a high-hemi, low lignin kraft pulp is dissolved in NMMO and either spunlaid, melt-blown or centrifugally spun into nonwovens.
Using "Super-Site" thinking once again, it is possible to envisage:
- A 350,000 tonne (i.e. similar to current polyester scale) lyocell plant linked to a source of low-cost dissolving pulp making a commodity "viscose replacement" fibre at polyester staple prices for a wide range of applications.
- A big spunlaid nonwoven line using dope from this fibre plant could make a wide range of biodegradable nonwovens including coverstock, backsheet and acquisition layer.
- These webs could be bonded in a variety of ways including hydroentangling on-line.
- Technology now in use to make the superabsorbent carboxymethylated Lyocell fibre could be used to make spun-laid cellulosic SAP's in-situ.
Direct dissolution of cellulose in Soda
It has been known for many years that wood-pulp partly dissolves in very cold dilute caustic soda, and there have been several attempts to improve such solutions to the point where textile fibres could be spun from the dope. Kamide et al working in Asahi's Fundamental (Fibre) Research Laboratory described fibres spun from soda solutions of cellulose (19). Here the key step was steam-explosion of the woodpulp to improve the accessability of the cellulose chains prior to contact with the sodium hydroxide.
Struszczyk et al (20) used cellulase enzymes to modify the structure of cellulose to allow it to dissolve in soda.
While these soda routes make fibres with properties inferior to viscose rayon, they are more than adequately strong for spun-laying or melt blowing. Once again this 'old' technology coupled with "Super Site" thinking could become the basis of a low-cost biodegradable nonwoven process.
Dissolution in Phosphoric Acid
Cellulose dissolves readily in 85% phosphoric acid without degradation and can be regenerated by spinning into water to make strong high modulus fibres. Reconcentration of the dilute phosphoric acid for reuse in dissolution has however been too expensive to allow an economic fibre process. It is therefore interesting to see in a recent series of patents from Akzo-Nobel, one postulating the centrifugal spinning of fibrous mats (21), another the manufacture of superabsorbent cellulose gel-fibres in hibrid form (22).
Direct Synthesis of Cellulose fibrils
Worthy of mention is the fact that bacteria, in this case Acetobacter Aceti produces fine fibrils of cellulose when cultured under the correct conditions. Weyerhauser commercialised Cellulon® fibrils based on this technology, later selling out to Monsanto. With filament diameters of less than 0.1 micron the fibres were hard to process even on wet-lay systems.
Discussion and Conclusions
Biodegradable thermoplastic fibres made from PLA have the potential to bring the production and marketing of biodegradable disposables one step nearer reality. Fibres of this sort appear spinnable on conventional melt spinning equipment into coverstocks that will work in conventional disposable diaper manufacturing plants. The ability to vary the properties of the PLA by careful selection of the blend of isomers and the polymerisation route appears to make it possible to vary the fibre properties from amorphous to crystalline thereby creating a range of melting points, biodegradation rates, fibre strengths, and even bicomponency.
Clearly the fibres can be used in a wide variety of applications and it will be interesting to see how the producers prioritise these applications. When sums of the order of $300m are spent on a polymer at the start of it's "learning curve" the economic pressure to develop the higher value applications first is enormous. In the case of PLA however the melting points appear to be similar to polypropylene rather than polyester, and its ability to replace polyester in conventional textiles could be similarly restricted.
In nonwovens, compared with the cellulosics, it has the key advantages of simple conversion into fibre and spunlaid nonwovens coupled with the resilience and bulk necessary for good surface dryness in coverstock. It appears to have the potential to beat current cellulosic nonwovens on price but we need to await actual prices of the product due to emerge from the 140,000 tonne plant in 2002 before we can be sure.
As for future cellulosic nonwovens, this year's announcements of PLA expansion reduces the already minimal likelihood of any investment in their really large scale manufacture either by the current technologies or by the visible future technologies linked to "Super Site" thinking.
References
- 1 Dumican B L, "Bioabsorbable Materials", Medical Textiles and Biomedical Polymers Conference, Clemson SC USA, 1989
- 2 Bonsignore PV et al, "Polylactic acid degradable plastics, coatings and binders" TAPPI Nonwovens Conference, Marco Island, 1992.
- 3 Wadsworth L et al, "Melt processing of PLA resin into nonwovens", 3rd Annual TANDEC Conference, Knoxville, 1993.
- 4 US Patent 5,702,826, Ehret P et al, Dec 30th 1997, assigned to Fiberweb.
- 5 P Ehret, "Deposa Nonwovens: Deposable disposables" INSIGHT 96 San Antonio.
- 6 Bogaert and Coszach, "Polylactic Acids: New polymers for novel applications" Speciality Polymers Session, Index99 Geneva.
- 7 The Dow Chemical Company, Press Release 11/1/2000.
- 8 Lunt J, Shafer, A, "Polylactic Acid Polymers from Corn: Potential Applications in the Textile Industry", Cargill Dow Polymers LLC, www.cdpoly.com.
- 9 "Biopol set to go commercial" Plastics and Rubber Weekly, 10 Jan 1987.
- 10 "Biopol: A Natural Plastic for a sustaninable environment" Monsanto Press Release 7th Oct 99
- 11 New Materials Japan - June 1997 pps 7-8.
- 12 "Biodegradable Spunlaid Fabrics" Medical Textiles - Sept 1996 pps 2-3.
- 13 USP 5,653,930 (Aug 5th 1997) Noda I., Lampe R, Satkowski M, assigned to Procter and Gamble.
- 14 USP 6,013,590 (Jan 11th 2000) Noda I., assigned to Procter and Gamble.
- 15 Skov Jensen H. The Super Site Concept - Really big airlaid machines for the prodution of baby diapers. Insight 99, San Diego.
- 16 "Fibres made by Wet Spinning of Cellulose Carbamate Solutions", Turenen et al, Neste Oy. TAPPI International Dissolving and Speciality Pulp Conference 1983.
- 17 Struszczyk H. Cellulose Carbamate and its utilisation. ACS, New Orleans, 1990.
- 18 Luo, Roscelli, Neogi, Sealy and Jewell "Lyocell fibres and compositions for making the same" WO 9947733 to Weyerhauser Sept 23rd 1999.
- 19 Kamide et al. "New Class of Cellulose Fibre spun from the novel solution of cellulose by wet-spinning method" J.App.Poly.Sci., 44,691-698 (1992).
- 20 Strusczcyk et al, "Celsol - Biotransformation of cellulose prior for fibre spinning" Cellucon 94, Bangor UK.
- 21 Westerlink, Maatman and Boerstoel, WO 97/28298 to Akzo Nobel, 7/8/97.
- 22 Westerlink, Maatman and Boerstoel, WO 97/30090 to Akzo Nobel, 21/8/97.